Why are HDPE pipes used for industrial applications?
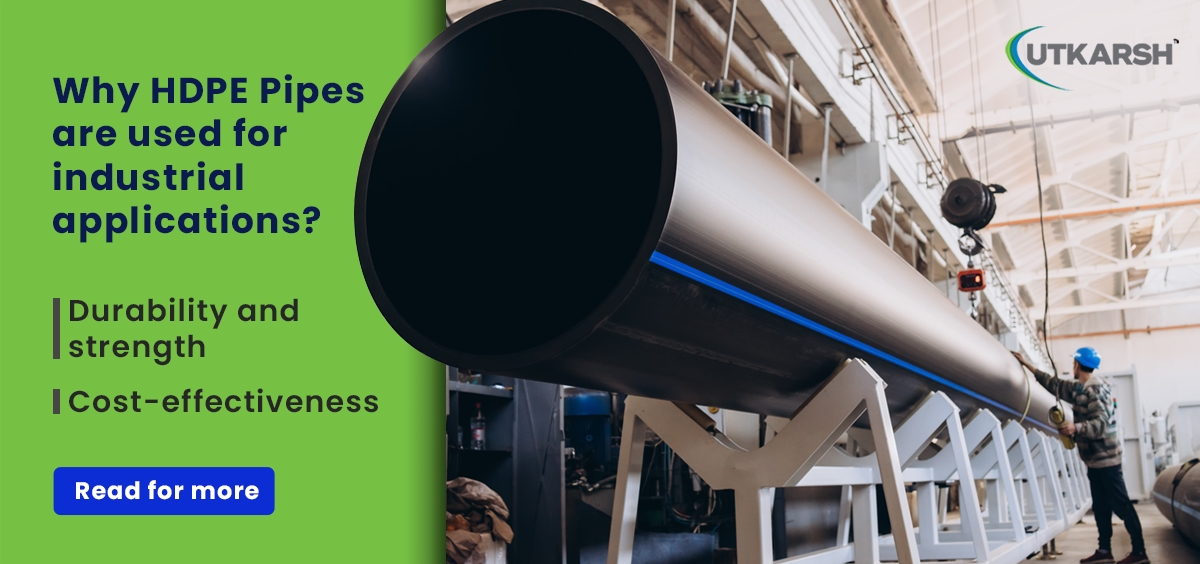
High-density polyethylene (HDPE) pipes have become a reliable, cost-effective, and environmentally friendly option for various industrial applications across multiple sectors. These pipes are extensively used in chemical processing plants, agriculture, construction sites, and many other industries due to their excellent chemical resistance, durability, and flexibility. Their ability to withstand extreme temperatures and harsh environmental conditions make them a preferred choice for many industries. As one of the leading HDPE pipe manufacturers, we share some of the useful insights on why HDPE pipes are used for industrial applications:
1. Durability and strength
HDPE pipes are known for their tensile strength, which is the resistance to breaking under tension. This property is important in industrial settings where pipes are often subjected to high pressure. The molecular structure of HDPE, characterised by its long polymer chains, contributes to the strength. These chains are tightly packed, which in turn, provides a high degree of resistance against internal and external pressures.
HDPE's flexibility is another significant benefit. Unlike rigid materials that can crack under stress, HDPE can bend without losing its structural integrity. The flexibility of HDPE is attributed to its semi-crystalline structure.
The corrosion resistance of HDPE further enhances its durability. Being a non-metallic material, it can withstand rust and corrosion.
2. Cost-effectiveness
The lightweight nature of HDPE reduces transportation and installation costs. Its ease of handling and installation are due to its weight and flexibility. It can be installed at a faster pace with less manpower compared to heavier, more rigid materials.
The minimal maintenance requirement of HDPE pipes is another aspect of their cost-effectiveness. Their resistance to corrosion, abrasion, and chemical attacks means that once installed, they require little maintenance, reducing long-term operational costs.
3. Other Benefits
HDPE's chemical resistance is an important feature in industrial applications where it is used for transport of harsh chemicals. It can safely transport various reactive materials without degradation, ensuring the integrity of both the pipe and the material being transported.
The smooth interior of HDPE pipes minimises friction losses, promoting a higher flow rate and reducing energy costs associated with pumping.
The environmental footprint of HDPE pipes is considerably lower than other materials. From production to disposal, HDPE pipes have a reduced impact on the environment, aligning with the sustainability goals of many industries.
Looking for a reliable HDPE pipe manufacturer?
Explore our HDPE pipes. We offer extensively tested products suitable for above-ground, floating, and subsurface marine uses. We have built strong relationships with key HDPE pipe dealers, which means that our products are both accessible and reliable. Key specifications of the products include:
- Standards: Meets IS:4984-2016, ISO:4427, EN 12201, IS:14151 (Parts I & II).
- Durability: Designed for a lifespan of 100 years.
- Features: Lightweight, easy transport, high 'C' value (150), smooth inner surface, crack-resistant, weather-resistant, excellent insulation.
Quality Testing:
- Tests for stripe, visual appearance, colour, reversion, melt flow rate (MFR), density, overall migration, carbon black content and dispersion, oxidation induction, elongation at break.