Hangars
Elevate your aviation facilities with our Pre-Engineered Buildings (PEBs), expertly crafted to meet the demanding requirements of modern hangars. With extensive experience in steel fabrication, we excel in delivering robust and versatile PEB solutions tailored for aircraft storage and maintenance. Our world-class capabilities allow us to handle a monthly steel fabrication of 25,000 MT and an annual steel supply of 300,000 MT, making us the best PEB manufacturer in India.
Our hangars are designed with the highest precision and adherence to standards such as IS, AISC, and MBMA. We utilise a 0.5 mm/0.6 mm thick multilayered hot-dip galvanised coating with a minimum yield strength of 345 MPa, ensuring exceptional durability and resistance to harsh environmental conditions. Each hangar features custom-designed structures that include crane beams, mezzanine systems, trusses, and more, all fabricated, tested, and finished in our comprehensive in-house facility.
Engineered for rapid construction and environmental efficiency, our PEB hangars offer an ideal solution for both military and commercial aviation needs. With a combination of superior design, flexibility, and reliability, our PEB hangars set a new standard for aviation infrastructure.
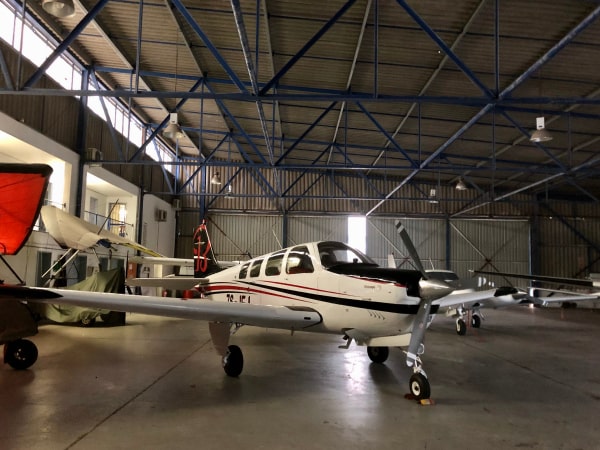
Manufacturing Process
Our meticulous, research-backed manufacturing process ensures durability, safety, and precision in every Pre Engineered Building.
-
Slitting of HR Coils
HR coils are split into desired widths according to the requirements.
-
Marking Plan (as per Fabrication Drawings)
The slit HR coils are marked according to the fabrication drawings.
-
Cutting of HR Plates through Plasma Cutting Machine
HR plates are cut using a plasma cutting machine, following the marked plan.
-
Continuous Welding (SAW) on One Side using PTW Machine
Continuous welding is performed on one side using a PTW machine with Submerged Arc Welding (SAW).
-
Stitch Welding (MIG) on Another Side using Rectifiers and Stick Electrodes
Stitch welding is performed on the other side using Metal Inert Gas (MIG) welding with rectifiers and stick electrodes.
-
Surface Preparation through Shot Blasting Machine
The welded sections undergo surface preparation using a shot blasting machine.
-
Application of Red Oxide Primer (for Synthetic Enamel Paint) / Epoxy Primer (for Epoxy Paint)
A red oxide primer or epoxy primer is applied depending on the type of final paint.
-
Application of Synthetic Enamel Paint / Epoxy Paint
Finally, synthetic enamel paint or epoxy paint is applied to the prepared sections.
Quality Policies
Discover our cutting-edge infrastructure and commitment to unparalleled quality standards.
-
Stringent Manufacturing Norms
We adhere to strict norms and certifications such as IS, BS, ASTM, AS, EN, OHSAS, MORTH, and SLS, ensuring quality and compliance in every aspect of our products.
-
State-of-the-Art Production Unit
Equipped with fabrication, testing, quality checks, galvanising, painting, logistics, and installation facilities, our production unit exemplifies innovation and quality, ensuring the highest standards are met for every pre-engineered steel building.
-
Expert Team
Our team of highly-trained specialists, experienced engineers, fabricators, and certified fitters ensures precision and craftsmanship in constructing steel structures, including roofing, exteriors, beams, and columns.
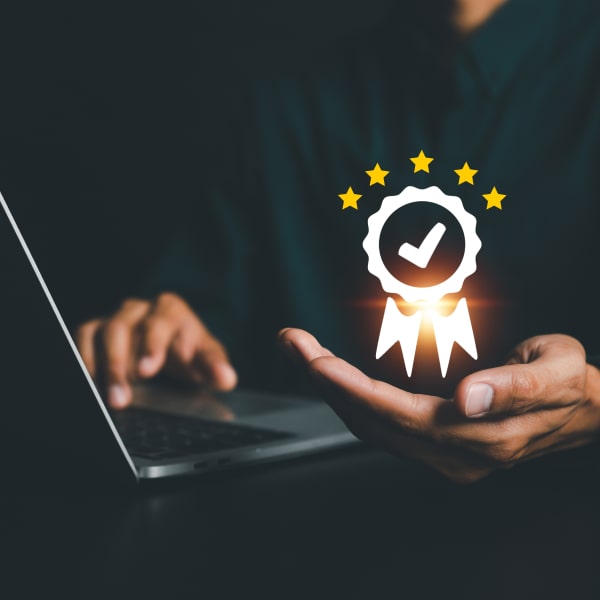
FAQs
Pre Engineered Buildings (PEBs) are structures that are designed, fabricated, and assembled using standardised components manufactured in a factory setting and then transported to the construction site for assembly. Unlike traditional construction methods, which involve on-site fabrication and assembly of structural components, PEBs offer faster construction timelines, cost savings, and greater design flexibility.
PEB structures offer several advantages that make them a preferred choice in construction projects. One major benefit is their faster execution, as they are built partially in a factory and then assembled on-site, expediting the project timeline. Additionally, they are cost-effective due to their construction in a controlled factory environment, resulting in savings in both time and money. PEB structures also require low maintenance, thanks to their use of durable materials like steel that resist rust and corrosion. This durability extends to their superior strength, allowing them to withstand harsh weather conditions and making them suitable for a wide range of applications, from warehouses to airport terminals and cold storage facilities.
Indeed, PEB structures are renowned for their strength and durability. When meticulously designed with premium materials, they exhibit resilience against earthquakes and various natural disasters. Nevertheless, the longevity of these structures hinges on several factors including: the intended purpose guiding their design, the quality of materials employed during manufacturing, the specific design elements incorporated into the PEB structures, and the advanced technologies utilised in their fabrication.
Pre-engineered steel buildings are composed of several key components that work together seamlessly. These include primary members or main frames, which form the structural backbone of the building, providing support and stability. Secondary members, often in the form of cold-formed members, complement the primary members and contribute to the overall structural integrity. Roof and cladding systems play a crucial role in protecting the building from environmental elements while also enhancing its aesthetic appeal. Additionally, deck accessories such as fasteners and connectors ensure that all parts of the building are securely connected and function as intended. Together, these components form a robust and efficient system that is well-suited for a variety of construction projects.
Pre Engineered Buildings (PEBs) offer a wide range of customisation options, including size, shape, design, layout, and finishes. Customers can choose from various roofing and wall systems, insulation options, doors, windows, and accessories to tailor the building to their specific requirements. Additionally, PEBs can be easily expanded or modified to accommodate future growth or changes in operational needs.
Our PEBs are primarily constructed using high-quality steel, which offers exceptional strength, durability, and versatility. The structural components of our PEBs, including columns, beams, and roof trusses, are fabricated from steel to ensure structural integrity and resistance to environmental factors.
The most common applications of pre-engineered buildings include office spaces, hangars, cold storage facilities, factories, plant buildings, airport sheds, railway car sheds, sports auditoriums, stadium structures, and multistoried steel buildings
With decades of high-end manufacturing experience, we stand a class apart from the competition. Our proven expertise in critical fabrication, and proud track record of having our products installed in mega projects worldwide, we are synonymous with quality, innovation and excellence in pre-engineered building solutions.
The construction timeline for Pre Engineered Buildings (PEBs) depends on various factors, including the size and complexity of the project, site conditions, and customisation requirements. However, PEBs typically have shorter construction timelines compared to traditional construction methods due to off-site fabrication and assembly of components. On average, PEB projects can be completed in a fraction of the time required for conventional construction, resulting in faster occupancy and return on investment for the client.
Utkarsh India maintains strict quality assurance measures throughout the design, fabrication, and installation process of Pre Engineered Buildings (PEBs). Our manufacturing facilities are equipped with state-of-the-art machinery and quality control systems to ensure that all components meet industry standards and specifications. Additionally, our experienced engineers and project managers oversee every aspect of the project to ensure compliance with quality and safety requirements.
Our PEBs are environmentally friendly and sustainable construction solutions. They require fewer resources and generate less waste compared to traditional construction methods, resulting in reduced environmental impact. Additionally, PEBs can incorporate energy-efficient features such as insulation, natural lighting, and renewable energy systems to further minimise their environmental footprint.
The Utkarsh India Steel brochure is available for download in PDF (Portable Document Format) files. Click here to access the available brochures and download them.
Use the ‘Contact Us’ link below to ask your question, and we'll do our best to respond to you as soon as possible.
Why Choose Utkarsh India
-
in steel fabrication, galvanisation, plastic extrusion and moulding, providing all infrastructural & manufacturing requirements under one roof.
-
along with cutting-edge testing facilities and R&D labs, and proven capability to accomplish manufacturing target deadlines.
-
for finished products and raw material storage, ensuring prompt availability and efficient supply chain management, with close connectivity via seaports, national highways and railways.
-
through raw material procurement from leading national and international manufacturers, ensuring responsible sourcing and superior traceability
-
with committed after sales support and assistance, ensuring seamless service and customer satisfaction at every step.
-
With forty years of experience in steel fabrication, galvanisation, plastic extrusion, and moulding, Utkarsh India is a leader in infrastructural manufacturing.
-
Our polygonal poles have undergone rigorous testing, including wind tunnel tests at IIT Kanpur and structural stability assessments from CSIR, Chennai, ensuring suitability for wind speeds up to 250 km/hr.
-
We produce 1000 lighting masts and 25,000 polygonal poles per month, leveraging well-trained manpower and advanced machinery. Our methodical process ensures timely delivery with minimal reworks and flawless finishes.
-
We have strategic procurement ties with SAIL and HZL for HR Coil and Zinc, and with various reputable companies for accessories. Our ready stock of materials ensures prompt production and delivery.
-
We utilise electroplated rope drums to combat corrosion and extend equipment life. All hardware is either made from stainless steel or hot-dip galvanised for enhanced durability.
-
Our five galvanising units employ a 7-tank process, using modern technology and supervised by qualified technicians, ensuring superior quality and longevity of the galvanised products.
-
Our in-house PU painting facility applies a protective and aesthetic coating over galvanised surfaces, enhancing product appearance and providing additional corrosion protection.
-
A dedicated logistics team oversees efficient transportation, with factories strategically located near NHAI, ports, and airports for seamless delivery.
-
Experienced service engineers provide comprehensive after-sales support, offering troubleshooting and technical assistance to ensure client satisfaction.
Related Videos
Explore more with our related videos, showcasing our products, manufacturing processes, solutions and more.