Substation Structures
Substation structures are the backbone of modern power transmission and distribution systems. These robust frameworks are essential for supporting and housing electrical equipment within a substation, including transformers, circuit breakers, busbars, and other critical components. Their primary function is to ensure the safe and reliable transfer of electrical energy from high-voltage transmission lines to lower-voltage distribution networks, ultimately powering homes, industries, and businesses. Without properly engineered substation structures, the integrity of the power grid could be compromised, leading to outages, inefficiencies, and safety risks.
Substation structures play a vital role in ensuring the stability and reliability of the power supply by supporting equipment that regulates voltage levels, controls power flow, and protects the grid from faults. Given their crucial function, these structures must possess several key features, including high durability, excellent corrosion resistance, and the ability to withstand extreme weather conditions and mechanical stresses. Substation structures must be designed with precision to accommodate various electrical components and provide easy access for maintenance and upgrades.
At Utkarsh India, we are committed to powering the future with our advanced substation structures. As a leading substation structure manufacturer in India, we bring over three decades of expertise in the design, fabrication, and supply of high-performance substation structures that cater to the evolving demands of power transmission and distribution. Our dedication to quality, precision, and innovation has established us as a trusted name in the industry, with a proven track record of delivering over 1,00,000 MT of substation and Transmission Tower structures to numerous prestigious projects.
Our substation structures are engineered to meet the stringent requirements of both Indian and international standards. By sourcing raw materials from reputed suppliers like SAIL, TATA, RINL, JINDAL, Hindustan Zinc, PGCIL Approved Sources, CORE Approved Sources, BIS Aproved Sources & others PSU/State Utility Approved Sources, we ensure that every component is built to withstand the challenges of modern power infrastructure. With six hot-dip galvanising facilities and an annual production capacity of 60,000 MT, we are equipped to handle large-scale projects with ease while maintaining swift response times, even for urgent demands.
At Utkarsh India, we understand that every project is unique. That’s why we offer customised solutions tailored to the specific needs of our clients. Our substation structures are not only designed for durability and corrosion resistance but are also versatile enough to support various applications, from power transmission to mounting substation equipment. Our commitment to delivering excellence extends to ensuring timely delivery and adherence to project specifications, making us the go-to partner for leading infrastructure companies and government departments.
As the demand for reliable power infrastructure continues to grow, Utkarsh India remains at the forefront of innovation in substation structure manufacturing. By consistently pushing the boundaries of engineering excellence, we are helping shape a sustainable, efficient, and resilient power grid for the future, and have established ourselves as the most trusted power substation supplier in india. Explore our range of substation structures and discover how we can power your next project.
Approved by Govt departments as well as infrastructure companies, our brand has been a part of several prestigious projects, nationally and globally, including PGCIL, UPPTCL, MPPTCL, KSEB, JUSNL, BSPTCL, OPTCL, AEGCL & more.
-
60000
Annual Production Capacity
-
6
Hot Dip Galvanising Facilities
- Raw materials conforming to IS 2062/BS EN 10025 or equivalent
- Raw Materials Dimensional confirming to IS 808,IS 1730
- Tolerance for Raw materials as per IS 1852
- Galvanisation Conforming to IS2629, IS6745,IS4759/ EN 1461
- Bolts - 4.6,5.6 & 8.8 Grade
- Specialised Design for Central & State Boards/End Clients Our substation structures are meticulously engineered to meet the specific requirements of state boards and end clients, ensuring optimal performance and compliance with regulations.
- Advanced Durability and Corrosion Resistance Built to withstand the toughest environmental conditions, our substation structures feature advanced durability and corrosion resistance, extending their lifespan and reducing maintenance needs.
- Premium-Grade Raw Materials We use only premium-grade raw materials sourced from reputed suppliers, ensuring that our substation structures meet the highest standards of quality and reliability.
- High Load-Bearing Capacity Designed for strength, our substation structures have a high load-bearing capacity, making them ideal for supporting heavy electrical equipment in power transmission and distribution systems.
- Customisable Designs for Versatility Our substation structures offer customisable designs that cater to a wide range of applications, ensuring flexibility and adaptability for diverse project requirements and client specifications.
- Hot-Dip Galvanised for a Longer Lifespan Our substation structures are hot-dip galvanised, ensuring superior corrosion resistance and extended lifespan, making them reliable for long-term power transmission infrastructure.
- Special High-Grade Zinc (Zn 99.995%) Material We use special high-grade zinc (Zn 99.995%) for galvanisation, ensuring top-quality protection against corrosion and enhancing the structural integrity of our substation structures.
- In-House Manufacture of All Components As the most trusted power substation manufacturer in India, we ensure complete control over quality by manufacturing all components in-house, providing consistency and reliability in every product.
- Prompt PAN India Delivery We offer prompt PAN India delivery, ensuring that our substation structures reach your project site on time, no matter where you are located.
- Adherence to National & International Standards Our substation structures comply with both national and international standards, guaranteeing safety, performance, and reliability in every project.
- Customisation Options as Per Customer Requirements We provide extensive customisation options, allowing our substation structures to meet your specific needs and ensuring optimal performance for your unique applications.
Product Application
Our substation structures serve diverse application areas, from power transmission to renewable energy integration, offering reliable support and safety solutions as a leading power substation manufacturer in India.
Our Projects
Market Growth
The global substation market, valued at USD 114 billion in 2022, is poised for substantial growth over the next decade. This expansion is driven by several key factors, including the electrification of off-grid areas and the increasing emphasis on renewable energy infrastructure. With the global push towards modernising energy systems, the substation market is experiencing a dynamic transformation. The forecasted compound annual growth rate (CAGR) of 3.4% from 2023 to 2032 reflects a robust demand for advanced substation structures. As countries invest heavily in expanding and upgrading their power grids, there is a growing need for reliable, high-performance substation solutions.
In particular, the integration of renewable energy sources is reshaping the market landscape. Substations play a crucial role in accommodating the fluctuating power output from solar and wind installations, ensuring efficient energy distribution and grid stability. This shift towards greener energy sources necessitates modern, adaptable substation structures that can support the evolving energy mix and enhance the resilience of power systems.
The market's growth is also influenced by ongoing infrastructure development projects. As urban and rural areas continue to expand, the demand for new and upgraded substations intensifies. This growth is further fueled by technological advancements, which drive improvements in substation design, efficiency, and safety. The global focus on enhancing energy infrastructure to meet increasing power demands underscores the need for high-quality, innovative substation solutions.
Overall, the increasing investments in energy infrastructure and the shift towards sustainable energy solutions position the substation market for significant expansion. This trend is set to continue as governments and industries prioritise the modernization of power systems to support growing energy needs and environmental goals.
Manufacturing Process
Our meticulous, research-backed substation structure manufacture process ensures the highest quality for substation structures, combining precision, safety, and durability at every stage.
-
Rinsing in Water Tank:
Post-pickling, materials are rinsed in water to neutralise remaining acid.
-
Dipping in Quenching Tank
Galvanised materials are cooled in a water quenching tank to solidify the coating.
-
Quenching Tank of Dichromate Water
Materials undergo passivation in dichromate water for enhanced corrosion resistance and improved finish.
-
Raw Material Procurement
Raw materials undergo rigorous QA/QC inspection, including chemical, mechanical, and dimensional checks, before fabrication to guarantee quality and performance.
-
Fabrication Work
- Cutting Materials are cut using hydraulic, power press, and CNC machines following QA/QC clearance.
- Punching & Drilling Holes are punched or drilled with precision, ensuring exact spacing and diameter, adhering to strict standards to prevent defects.
- Welding Limited welding is performed before galvanising, using approved electrodes and ensuring full penetration and defect-free welds by qualified welders.
- Bending High-strength structural steel is bent hot to prevent deformation, and members are cooled naturally.
- Marking/Stamping Members are marked for identification during erection, using metal dye to ensure visibility post-galvanization.
-
Degreasing Tank
Fabricated materials are immersed in a degreasing tank to remove impurities and surface scale.
-
Pickling in Acid Tank
Materials are pickled in an acid tank to clean and prepare the surface for galvanization.
-
Pre-fluxing
A flux solution is applied to enhance zinc coating adhesion.
-
Drying in Hot Chamber
Materials are dried in a hot chamber to eliminate moisture before galvanization.
-
Hot Dip Galvanisation in Zinc Bath
Materials are immersed in a hot zinc bath for uniform coating.
-
Finishing
Finished materials are inspected, trimmed, and prepared for bundling and dispatch, ensuring they meet all quality standards.
Quality Policies
At Utkarsh India, our quality policy emphasises advanced infrastructure, stringent quality control, and high production capacity, ensuring the highest standards in substation structures and tower materials.
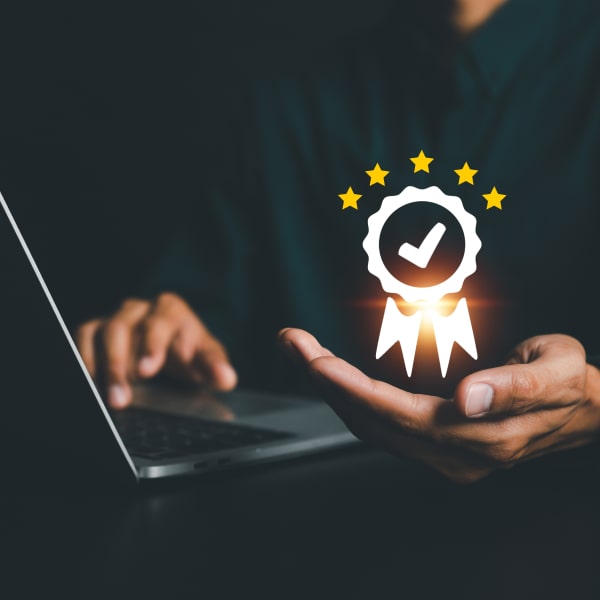
FAQs
A substation is a crucial part of the electrical grid that transforms voltage levels for efficient power distribution.
Key components include transformers, circuit breakers, switchgear, busbars, and protection systems.
Substations enable the integration of renewable energy sources like solar and wind power into the grid.
Considerations include capacity requirements, voltage levels, reliability, environmental factors, and compliance with standards.
GIS offers compact size, enhanced safety, and reduced maintenance compared to traditional AIS (Air-Insulated Switchgear).
We adhere to rigorous quality control measures, conduct advanced testing, and comply with international standards like ISO 9001.
Environmental considerations include noise reduction, emissions control, and eco-friendly materials for sustainable operation.
They enhance grid stability, minimise downtime through advanced protection systems, and support efficient fault management.
Substations facilitate data communication, real-time monitoring, and automation, essential for smart grid functionality.
We offer tailored solutions, collaborate on design specifications, and provide expert consultation throughout the project lifecycle.
Our substation structures feature advanced durability, corrosion resistance, and are built to meet national and international standards with customization options.
We leverage cutting-edge technology and efficient manufacturing processes to meet the increasing global demand for high-quality substation structures and solutions.
Advanced technology enhances precision, quality, and efficiency in the manufacturing process, ensuring our substation structures meet the highest industry standards.
Our commitment to quality, adherence to international standards, and innovative manufacturing processes position us as a top substation structure manufacturer in India.
Why Choose Utkarsh India
-
With forty years of experience in steel fabrication, galvanisation, plastic extrusion, and moulding, Utkarsh India stands out as a leader in infrastructural manufacturing.
-
Our cutting-edge design capabilities and advanced R&D laboratories are complemented by state-of-the-art in-house testing facilities, ensuring innovative solutions and rigorous quality control.
-
We maintain a substantial stock holding area for both finished products and raw materials, guaranteeing prompt availability and efficient supply chain management.
-
Raw materials are sourced through MOUs with leading national and international manufacturers, ensuring the highest quality standards in our products.
-
Our robust financial position enables us to meet manufacturing deadlines and fulfil large-scale projects efficiently.
-
Utkarsh India provides a one-stop solution for all infrastructural needs, making us the preferred partner for both public and private sector projects.
-
Our manufacturing units are well-connected via seaports, national highways, and railways, facilitating smooth and timely delivery.
-
We excel in managing vendor relationships, supported by dedicated after-sales assistance and support.