Ohe Structures
Overhead Electrification (OHE) structures are critical components in railway systems, responsible for delivering electrical power to trains through overhead lines. These structures, including TTC Mast and B-Series Mast, RSJ Mast, BFB Mast, Portal, and SPS along with TSS & SSP, are integral to railway electrification as they hold and maintain the electrical cables that power trains. OHE mast in railway ensures efficient and reliable energy transmission, enabling high-speed rail networks, suburban transit systems, and metro lines to operate smoothly and efficiently. The design and quality of these components are crucial for maintaining consistent power supply and operational safety.
In railway electrification, the importance of OHE structures cannot be overstated. They must be robust and durable, capable of withstanding various environmental conditions, including weather and mechanical stress. Essential features of effective OHE mast in railway include high-quality materials, excellent corrosion resistance, precise engineering, and adherence to stringent industry standards. These features ensure the longevity and reliability of the infrastructure, which is vital for uninterrupted rail services.
At Utkarsh India, we proudly lead the way in manufacturing advanced railway electrification structures, integral to the core of modern railway systems. Our TTC Mast and B-Series Mast, RSJ Mast, BFB Mast, Portal, and SPS along with TSS & SSP are essential components in core railway electrification, designed to meet the highest standards of performance and reliability. These masts are pivotal in supporting the overhead electrification systems that power today's rail networks, ensuring seamless and efficient power distribution across diverse railway applications.
The TTC Mast exemplifies our commitment to quality in OHE masts in railway systems. Standing at a standard height of 10.135 metres with booms available in lengths of 5.5 metres and 8.0 metres, it is manufactured from high-quality hot-dip galvanised steel. The galvanisation process, with coatings of 610 GM/SQM or 1000 GM/SQM, offers superior resistance to corrosion and environmental wear. Built to site-approved specifications and adhering to RDSO and IS standards, the TTC Mast is a cornerstone in ensuring the durability and reliability of overhead electrification infrastructure.
Complementing the TTC Mast, our B-Series Mast provides versatile and robust solutions for various railway projects. Available in models such as B-150, B-175, B-200, B-225, and B-250, and featuring a standard height of 9.5 metres with customisable lengths, the B-Series Mast is designed to meet the demanding requirements of modern rail systems. Its high-quality hot-dip galvanisation ensures excellent corrosion resistance and long service life, while its compliance with RDSO and CORE drawing approvals guarantees consistent and reliable performance.
Other Over head electrification structures:
RSJ Mast: The RSJ Mast is a robust and reliable structure used extensively in railway electrification projects. Made from high-strength materials, it is designed for heavy-duty applications, providing the necessary support for overhead lines in challenging environmental conditions. Its hot-dip galvanization ensures excellent corrosion resistance, ensuring long-term durability and performance.
BFB Mast: The BFB Mast (Broad Flange Beam Mast) offers a sturdy and durable solution for railway electrification. Engineered for high load-bearing capacity, it is ideal for supporting overhead electrical cables across long spans. Manufactured from galvanised steel, the BFB Mast ensures superior weather resistance and structural integrity, adhering to the highest industry standards.
Portal: The Portal structure is designed to span across multiple tracks, providing comprehensive support for overhead electrical lines in railway systems. It is particularly suited for areas with complex track arrangements or multiple overhead lines. Built from high-quality galvanised steel, the Portal structure ensures stability, strength, and resistance to environmental wear.
SPS (Steel Pole Structure): The SPS is a versatile and cost-effective solution for railway electrification, offering support for overhead lines in various rail applications. With its compact design and hot-dip galvanization, the SPS provides durability and corrosion resistance, making it a reliable choice for both urban and rural rail projects.
TSS (Traction Substation) & SSP (Sectioning and Paralleling Post): TSS and SSP structures are critical components in the power distribution network of railway systems. The TSS is responsible for supplying and regulating power to overhead lines, while the SSP ensures proper sectioning and paralleling of the electrical system. Both structures are built to meet the highest safety and performance standards, ensuring efficient power transmission and operational reliability.
Together, the TTC Mast, B-Series Mast and other masts from Utkarsh India represent the pinnacle of quality in railway electrification. Whether for mainlines, suburban transit, or metro systems, our masts provide the necessary support and stability for efficient and reliable railway operations. Explore our range of masts to find the ideal solution for your railway electrification needs.
-
48000
Cumulative Production Capacity
-
30000
Mast and TTC Production Capacity
Supply Range
- Construction - Over head electrification structure
- Attachment - As per site approved design
- Body - Hot Dip Galvanised (610 GM / SQM or 1000 GM / SQM)
- Height - 9.5 m Standard Length / Beyond 9.5m Section (Custom)
- Drawing - As per RDSO (Ref No. ETI C 0071)
- Specification - IS-2062, IS-808
- STR - CORE-STR-01
- Drawing - As per RDSO (Ref No. ETI C 0009 69, R B SH-3, ETI C 0009 69 R B SH-1, ETI C 0009 69 R C SH-2, ETI C 0009 69 R C SH-5, ETI C 0009 69 RC SH-4)
- Specification - IS-2062, IS-808
- STR - CORE-STR-01
PORTAL
Supply Range
- Construction - Over head electrification structure
- Attachment - As per site approved design
- Body - Hot Dip Galvanised (610 GM / SQM or 1000 GM / SQM)
- Height - Based on type of the Portal, i.e., O Type, N Type, R Type, G Type, S Type etc.
- Drawing - As per RDSO (Ref No. ETI C 0017 70 R B SH-4, ETI C 0017 70 R B SH-5, ETI C 0011 69 SH 5, ETI C 0011 69 SH 6, ET IC 0017 70 RB SH-2, ETI C 0008 R A SH-1, ETI C 0008 R B SH-2, ETI C 0008 R B SH-4, ETI C 0008 R C SH-3, ETI C 0008 R C SH-5, ETI C 0008 RA SH-6, ETI C 0011 69 R C SH-1, ETI C 0011 69 R C SH-2, ETI C 0011 69 SH-4, ETI C 0017 70 R A SH-1, ETI C 0017 70 R A SH-6, ETI C 0017 70 R B SH-3)
- Specification - IS-2062, IS-808
- STR - CORE-STR-01
SPS
Supply Range
- Construction - Over head electrification structure
- Attachment - As per site approved design
- Body - Hot Dip Galvanised (610 GM / SQM or 1000 GM / SQM)
- Height - Fitting accessories for Mast, TTC & Portals
- Drawing - As per RDSO (Ref No. ETI C 0076 Rev. C, ETI OHE P 3231, ETI OHE P 3121, etc.)
- Specification - IS-2062, IS-808
- STR - CORE-STR-01
TSS
Supply Range
- Construction - Traction Substation Structure
- Attachment - As per site approved design
- Body - Hot Dip Galvanised (610 GM / SQM or 1000 GM / SQM)
- Height - As per specification
- Drawing - As per RDSO (Ref No. ETI/ C/ 0310 to 390)
- Specification - IS-2062, IS-808
- STR - CORE-STR-01
- Hot-Dip Galvanised Ensures long-lasting corrosion resistance for our OHE masts in railway, critical in railway electrification structures. Hot-dip galvanisation provides exceptional durability, extending the service life of OHE masts in railway systems.
- Customisable Heights Standard height with options for custom lengths to meet specific project needs. Our railway electrification solutions offer flexible solutions tailored to diverse infrastructure requirements.
- Site-Specific Attachments Tailored as per site-approved designs for effective implementation. Ensuring our core railway electrification structures meet exact specifications, providing reliable support for complex railway networks.
- High-Quality Steel Manufactured from high-quality steel that complies with IS-2062 and IS-808 standards. Our railway electrification structures ensure superior performance and longevity, meeting industry standards.
- Robust Construction Designed for overhead electrification, offering durability and strength. Our OHE masts in railway systems are engineered to withstand harsh conditions, ensuring reliable power delivery and infrastructure integrity.
- Long-Term Durability Hot-dip galvanisation provides these masts with superior corrosion resistance, crucial for railway electrification structures. This ensures long-term durability and reliability in harsh environmental conditions.
- Custom Fit With adjustable heights and boom lengths, these masts are designed to fit specific site requirements. This flexibility supports diverse core railway electrification needs, making us a top OHE structure manufacturer in India.
- Enhanced Safety Our robust construction ensures these masts are safe and reliable for overhead electrification. The design meets stringent standards, supporting secure and efficient railway electrification projects.
- High Load Capacity Constructed from high-quality steel, these masts offer exceptional strength and support. This high load capacity ensures dependable performance in railway electrification structures and supports extensive railway networks.
- Ease of Installation Site-specific attachments streamline the installation process for these masts, ensuring efficient setup. Our solutions are designed to meet the unique needs of core railway electrification projects, facilitating hassle-free deployment.
Product Application
Our OHE structures are integral to various railway electrification projects, delivering robust support and stability for overhead electrification systems across diverse railway infrastructures. As a leading OHE structure manufacturer in India, we cater to all needs efficiently.
Our Projects
Market Growth
The global rail components market experienced significant growth, valued at USD 78 billion in 2020. Projections indicate this market will expand to USD 95 billion by 2026, reflecting a steady compound annual growth rate (CAGR) of over 3%. This growth is driven by the increasing demand for railway infrastructure upgrades and advancements in railway technology, including the adoption of more efficient and durable railway electrification structures.
In particular, the railway rolling stock market is poised for substantial growth, anticipated to reach USD 6.43 billion by 2034, up from USD 3.87 billion in 2024. This expansion highlights a strong investment trend in the development and modernization of rail vehicles, which complements the broader railway infrastructure improvements. The surge in rolling stock investments aligns with global initiatives to enhance the efficiency and capacity of rail networks.
A key component of this growth is the demand for diverse OHE masts in railway. Masts are classified into categories such as A, B, C, E, and H, each designed to support different types of overhead electrification equipment. This classification reflects the customization and versatility required to meet the specific needs of various rail projects, from mainline routes to specialised industrial applications.
The railway electrification sector is increasingly focusing on robust, high-quality structures that ensure reliability and safety in power transmission. As the industry evolves, the emphasis on advanced railway electrification structures will drive innovation and investment, creating opportunities for companies specialising in OHE mast manufacturing. This ongoing development underscores the critical role of modern infrastructure solutions in supporting the future of global rail networks.
Manufacturing Process
Our systematic and state-of-the-art manufacturing process for railway electrification structures is designed to meet customer expectations and ensure the highest level of satisfaction.
-
Receipt of Purchase Order
Upon receiving the purchase order, it is reviewed and analysed to ensure alignment with project requirements.
-
Material Management
Drawings are thoroughly reviewed and cross-checked for any discrepancies, which are resolved with client approval. The Bill of Materials (BOM) is then prepared to initiate the procurement process.
-
Raw Material Procurement
Raw materials are procured based on indent records, ensuring adherence to required specifications and quality standards.
-
Raw Material Inspection
Raw materials are inspected at the supplier's premises by RITES. Upon receipt, they undergo further in-house quality checks to validate compliance with standards.
-
Production Planning
Job cards are generated to outline the production schedule and allocate resources efficiently.
-
Fabrication Process
Our fabrication process includes several operations:
- Cutting: Performed using hydraulic shearing machines or oxy-fuel cutting to achieve precise results.
- Punching: Utilises a punch press to create holes via shearing.
- Drilling: A rotary cutting process to bore holes in solid materials.
- Stamping: Sheet-metal forming process that involves punching, embossing, and coining.
- Fitting: Joining multiple materials of different sections and sizes.
- Welding: A high-temperature process to fuse metals, forming strong joints.
- Finishing: Removing weld spatters, grinding rough edges, and completing the materials in their black stage.
-
In-process Inspection
Throughout the fabrication process, operations such as cutting, punching, drilling, stamping, fitting, and welding are inspected to ensure quality.
-
Mass Production
Once the initial phases pass inspection, mass production begins to meet project demands.
-
Surface Treatment
The transition from raw to finished products involves the following surface treatment steps:
- Pickling in Caustic Soda Solution: Removes impurities and scales from the surface.
- Rinsing in Water House: Removes residual caustic solution.
- Pickling in Acid Tank: Further cleaning and preparation for galvanization.
- Rinsing in Water Tank: Neutralises any remaining acid.
- Pre-fluxing: Applies flux to aid zinc adhesion.
- Drying in Hot Chamber: Prepares materials for galvanization by removing moisture.
- Hot Dip Galvanization in Zinc Bath: Ensures uniform zinc coating on the surface.
- Cooling in a Quenching Tank of Running Water: Cools the galvanised materials.
- Cooling in Quenching Tank of DI-Chromate Water: Enhances corrosion resistance and surface finish.
- Finishing: Inspects and trims the materials before roll forming.
-
Quality Control
Visual and coating inspections are conducted to ensure the finished materials meet the required standards.
-
Final Inspection and Dispatch
After passing all quality checks, the finished materials undergo a final inspection before being dispatched to the customer, ensuring compliance with project requirements.
Quality Policies
At Utkarsh India, we uphold the highest standards in every product, focusing on rigorous quality control and continuous improvement to deliver exceptional railway electrification solutions.
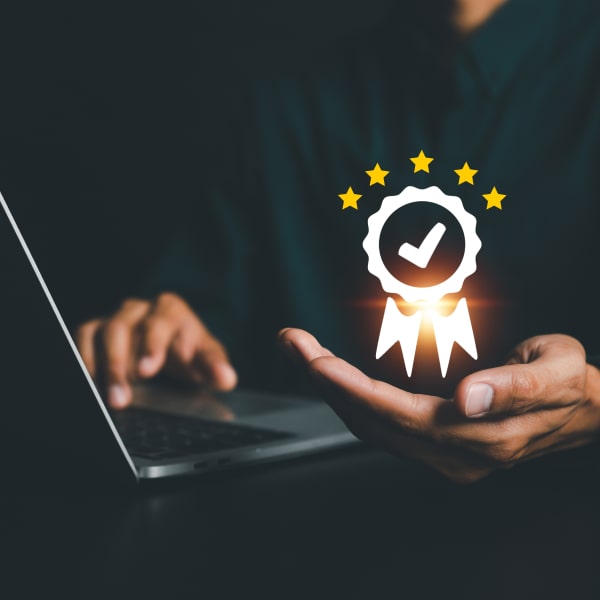
FAQs
An OHE (Overhead Electrification) structure is a key component in railway systems, designed to support and maintain the overhead electrical lines that power trains. It ensures efficient power transmission across railway networks.
OHE structures are used in various railway applications, including mainlines, suburban rail, industrial rail, freight corridors, and metro systems, providing essential support for overhead electrification systems.
Essential features of OHE structures include high corrosion resistance (through hot-dip galvanisation), customizable heights, site-specific attachments, compliance with standards (IS-2062, IS-808), and robust construction for reliability.
OHE structures play a crucial role in railway electrification by supporting the overhead electrical lines necessary for powering trains, ensuring consistent power delivery and system efficiency across different rail applications.
OHE masts in railway are typically made from hot-dip galvanised steel, which offers excellent corrosion resistance and long-term durability. This material is crucial for maintaining the integrity of the overhead electrification systems.
Common types of OHE masts include TTC Masts, B-Series Masts, and other classifications depending on drilling holes and support requirements for different OHE equipment and railway applications.
Yes, OHE structures can be customised to meet specific project requirements, including adjustments in height, boom lengths, and additional features, ensuring adaptability for various railway electrification projects.
Hot-dip galvanisation provides OHE structures with superior corrosion resistance, ensuring extended service life and reduced maintenance needs, which is essential for the harsh conditions of railway environments.
OHE structures should comply with RDSO specifications and IS standards (such as IS-2062 and IS-808) to ensure they meet the necessary performance, safety, and reliability requirements for railway electrification.
Why Choose Utkarsh India
-
With forty years of experience in steel fabrication, galvanisation, plastic extrusion, and moulding, Utkarsh India stands out as a leader in infrastructural manufacturing.
-
Our railway electrification structures feature expert engineering, ensuring reliable and efficient performance for diverse rail systems and applications.
-
We use high-quality steel and aluminium alloys, providing durability and corrosion resistance to withstand challenging environmental conditions.
-
Our advanced manufacturing process includes precise fabrication and rigorous quality checks, guaranteeing top-notch performance and adherence to industry standards.
-
We apply innovative surface treatments like galvanisation, enhancing corrosion resistance and extending the lifespan of our railway electrification structures.
-
We implement comprehensive quality control measures throughout production, ensuring each structure meets stringent safety and performance standards.
-
With extensive market expertise, we understand the latest trends and requirements, positioning us as a leader in railway electrification solutions.
-
Our customer-centric approach focuses on tailored solutions, addressing specific needs and providing exceptional support throughout the project lifecycle.