Railway Electrification Structures
Railway electrification structures are essential components that support the efficient operation of electrified rail networks. These structures include various types of masts, portals, and supporting steel frameworks, all of which are designed to hold overhead equipment (OHE) such as wires and catenary systems that supply electrical power to trains. The reliability and durability of these structures are crucial for ensuring the uninterrupted flow of electricity, enabling trains to operate smoothly and safely across vast distances. In an era where railways are increasingly transitioning to electrified systems, the role of these structures cannot be overstated.
The uses of railway electrification structures extend beyond just supporting overhead wires. They play a vital role in stabilising the rail network, especially in challenging environments such as tunnels, bridges, and urban areas with complex track layouts. Additionally, these structures are integral to Traction Substations (TSS), which convert high-voltage AC power into the voltage needed for train operations.
The importance of these structures lies in their ability to withstand extreme weather conditions, maintain structural integrity over long periods, and ensure the safety of both the railway infrastructure and the passengers it serves. Must-have features for railway electrification structures include high corrosion resistance, precise engineering for specific load requirements, and compliance with rigorous industry standards like those set by CORE and RVNL.
Utkarsh India, a leader in railway electrification structure manufacturing, plays a pivotal role in modernising the nation's rail infrastructure. As a CORE-approved Part I manufacturer, we offer a comprehensive range of railway electrification structures, including RSJ Masts, BFB Masts, B-Series Masts, TTC Masts, Portal, ERC, SPS & OHE Structures and various types of Portals, among others. Our commitment to quality and innovation enables us to deliver future-ready solutions that ensure the efficiency and safety of railway operations across India. With extensive expertise and state-of-the-art facilities, we have established ourselves as a trusted railway electrification structure supplier in India.
Our world-class manufacturing facilities, located on NH6 in Jangalpur and NH2 in Gurap, West Bengal, are equipped with advanced technology and stringent quality control processes. Spread over 100 acres, our plants feature over 30 lakh square feet of covered shed area and include Six in-house 12.5-meter-long hot-dip galvanising units. These facilities allow us to produce up to 4,000 metric tons of railway electrification structures per month, ensuring timely delivery of high-quality products. Our steel structures are made with Special High-Grade Zinc (99.995% purity) from Hindustan Zinc Limited, ensuring superior corrosion resistance and longevity.
As leading railway electrification structure manufacturers, we source steel exclusively from SAIL or CORE-approved re-rollers & Renowned Brands using SAIL material. This ensures that our products meet the highest standards of quality and durability. Our strict quality assurance and quality control processes ensure that every piece undergoes rigorous inspection at various stages, from raw material procurement to final dispatch. This attention to detail allows us to consistently deliver error-free products that meet our clients' exact specifications.
At Utkarsh India, we pride ourselves on being a reliable railway component maker, serving both national and global clients. Our strategic location, advanced logistics department, and dedication to customer satisfaction enable us to provide cost-effective transportation solutions, ensuring that our railway steel structures reach their destinations on time. Whether it's supporting overhead equipment (OHE) or providing robust foundations for Traction Substations (TSS), our railway electrification structures are engineered to meet the dynamic demands of the industry, contributing to a safer and more efficient railway network across India.
-
48000
Combined Production Capacity
-
30000
Mast and TTC Production Capacity
-
18000
Portal and Sps Production Capacity
- Robust Construction Materials Our railway electrification structures use high-grade steel sourced from SAIL and re-rollers & renowned brands ensuring durability and strength for reliable performance in railway systems.
- Advanced Hot-Dip Galvanization Each component is hot-dip galvanised with special high-grade zinc, offering superior corrosion resistance and longevity for railway electrification structures exposed to harsh environments.
- Precision Engineering Standards We adhere to CORE and RVNL standards for all masts and structures, ensuring precision in design and manufacturing for seamless integration into railway electrification systems.
- Comprehensive Testing Protocols Our in-house testing facilities follow rigorous protocols, including IS and ETI guidelines, ensuring each structure meets quality and safety standards before deployment.
- Efficient Inspection Processes Our QA/QC team conducts thorough inspections at various stages, including raw material procurement and production, to ensure flawless quality and adherence to specifications.
- Customised Design Options We offer tailored solutions for diverse railway needs, including RSJ and BFB Masts, Portals, and TSS, catering to specific project requirements and site conditions.
- Rapid Production Capacity With a production capacity of 48,000 MT per annum, we meet high-volume demands efficiently, ensuring timely delivery of railway electrification structures across projects.
- Durable Materials Our railway electrification structures use high-grade steel and special zinc coatings for enhanced durability, ensuring long-lasting performance in various environmental conditions.
- Advanced Galvanisation We employ hot-dip galvanisation with 99.995% pure zinc to prevent corrosion, meeting stringent standards for railway steel structures and extending the lifespan of components.
- Precision Engineering Each component of our railway electrification structures is manufactured to exact specifications, adhering to CORE and RVNL guidelines to guarantee superior quality and reliability.
- Rapid Inspection Our in-house testing and rapid inspection processes, with results within 20-25 days through RITES, ensure compliance with quality standards for railway electrification structures.
- Customised Solutions We offer bespoke designs for various railway components, including RSJ Masts and Portals, tailored to specific project requirements and ensuring optimal functionality for rail networks.
- Robust Support Our structures provide robust support for Overhead Equipment (OHE) and Traction Substations (TSS), ensuring effective electrical power distribution and operational efficiency across the rail network.
- Certified Standards We adhere to certified standards, including IS 802 and IS 2629, ensuring our railway electrification structures meet rigorous industry requirements for performance and safety.
- Enhanced Product Longevity Our railway electrification structures are engineered for long-lasting performance, using high-grade materials and advanced galvanisation to withstand harsh environmental conditions.
- Advanced Galvanisation Utilising special high-grade zinc, our hot-dip galvanisation process ensures exceptional corrosion resistance, extending the lifespan of steel railway structures and reducing maintenance needs.
- Custom Solutions We offer tailored railway electrification structures to meet specific project requirements, ensuring optimal fit and performance for various rail applications and environments.
- Robust Construction Designed for resilience, our steel railway structures provide reliable support for overhead equipment and traction substations, ensuring stable and efficient power distribution across the rail network.
- High Production Capacity With a monthly production capacity of over 4000 MT, including significant quantities of portals and SPS, we efficiently meet large-scale project demands and timelines.
- Quick Delivery Our efficient logistics and raw material procurement processes enable prompt delivery of railway electrification structures, minimising project delays and ensuring timely completion.
- Comprehensive Testing All products undergo rigorous testing at our NABL-approved facilities, ensuring they meet stringent quality standards and are ready for reliable performance in critical railway applications.
Market Growth
The global Railway Electrification Systems market is poised for significant growth, with projections indicating a rise to USD 18,760 million by 2028, up from USD 17,000 million in 2021. This growth translates to a steady compound annual growth rate (CAGR) of 1.4% from 2022 to 2028. China leads the market with the largest share, accounting for nearly 27%, while Germany holds the second-largest position. This trend reflects the increasing global emphasis on modernising railway infrastructure to enhance efficiency and safety.
In terms of overall market size, it is expected that the Railway Electrification Systems market will reach USD 18,400 million by 2028, growing at a CAGR of 1.5% over the analysis period. This growth is driven by various factors, including substantial investments in railway development and increasing demand for safer and more efficient transport systems. The continued expansion of railway networks and advancements in electrification technologies play a crucial role in meeting the rising passenger and freight capacity requirements.
Since 2014, the global railway electrification landscape has seen significant progress, with approximately 38,650 kilometres of electrified railway tracks achieved up to October 2023. This substantial growth underscores the global commitment to enhancing rail transport efficiency and environmental sustainability. The expansion of electrified rail networks contributes to reducing reliance on non-renewable energy sources and supports the transition to greener transportation alternatives.
However, the market faces challenges that may impact growth. High capital requirements and the lack of consistent technological infrastructure, particularly in developing countries, pose significant barriers. Additionally, the high costs associated with overhauls and maintenance can be a deterrent for investment in railway electrification systems. Addressing these challenges is essential for sustaining the growth of the market and achieving long-term improvements in global railway infrastructure.
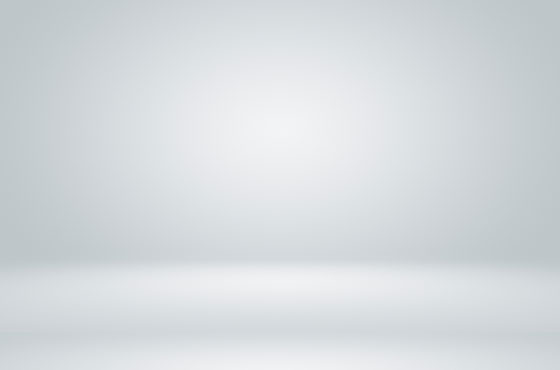
Manufacturing Process
-
Receipt of Purchase Order
Upon receiving the purchase order, it undergoes a thorough review and analysis to ensure that it aligns with the specific project requirements.
-
Material Management
Detailed drawings are reviewed and cross-checked for any discrepancies. Any issues are resolved with the client’s approval, and a Bill of Materials (BOM) is prepared to initiate the procurement process.
-
Raw Material Procurement
Raw materials are procured based on indent records, ensuring that they adhere to the required specifications and quality standards.
-
Raw Material Inspection
At the supplier's premises, raw materials are inspected by RITES. Upon receipt at our facility, the materials undergo rigorous in-house inspections to ensure compliance with standards.
-
Production Planning
Job cards are generated to outline the production schedule and efficiently allocate resources, ensuring smooth workflow and timely delivery.
-
Fabrication Process
The fabrication process involves several operations:
- Cutting: Utilises hydraulic shearing and oxy-fuel processes for precise material cutting.
- Punching: Involves creating holes in materials through a shearing process.
- Drilling: Employs rotary cutting tools to bore holes in solid materials.
- Stamping: Forms metal sheets into desired shapes using stamping presses.
- Fitting: Joins multiple materials on designed Zigs as per approved drawings.
- Welding: Fuses materials by melting the base metal and adding filler for strength.
- Finishing: Removes weld spatters, grinds rough edges, and chips slags for a clean finish.
-
In-process Inspection
Throughout the fabrication, each operation is closely monitored for quality assurance, ensuring that the final product meets all standards.
-
Mass Production
Once the initial phases are completed satisfactorily, mass production begins to meet the project demands.
-
Surface Treatment
The materials undergo a series of surface treatments, including:
- Pickling in Caustic Soda Solution: To remove impurities and scale.
- Rinsing in Water House: To remove residual caustic soda.
- Pickling in Acid Tank: Further cleaning and preparation for galvanization.
- Pre-fluxing: Application of flux solution to aid zinc coating adhesion.
- Drying in Hot Chamber: Removal of moisture before galvanization.
- Hot Dip Galvanisation: Immersing materials in a zinc bath for uniform coating.
- Cooling: Quenching in running water and DI-chromate water for corrosion resistance.
-
Quality Control
Visual and coating inspections are performed to verify the quality of the finished materials, ensuring they meet all specified standards.
-
Final Inspection and Dispatch
After passing all quality checks, the finished materials undergo final inspection before dispatch, ensuring full compliance with project requirements.
Quality Policies
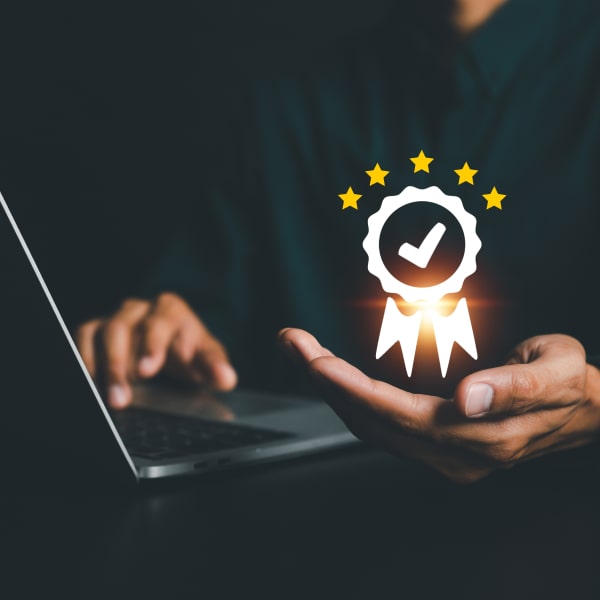
FAQs
Railway electrification structures are essential components that support the electrical systems of railways, including overhead lines, masts, and support structures, enabling efficient train operations.
Railway electrification is crucial for enhancing the efficiency, safety, and environmental sustainability of rail transport by providing a reliable source of power for trains, reducing reliance on fossil fuels.
Essential features include high durability, compliance with safety standards, corrosion resistance, and compatibility with various railway systems to ensure optimal performance and longevity.
High-quality steel and aluminium alloys are commonly used due to their strength, durability, and resistance to environmental conditions, ensuring long-lasting performance in railway electrification systems.
The manufacturing process involves detailed steps, including material procurement, fabrication, surface treatment, and rigorous quality control to ensure each structure meets industry standards.
Benefits include increased operational efficiency, reduced maintenance costs, lower environmental impact, and enhanced safety and reliability of railway transport systems.
The global market for railway electrification systems is projected to grow significantly, driven by increased demand for efficient and safe rail transport solutions across various regions.
Quality policies ensure that all railway electrification structures meet stringent standards for safety, durability, and performance, through strict inspection and compliance testing processes.
Common applications include supporting overhead line systems, masts, and other infrastructure necessary for electrifying railway networks, ensuring efficient power supply to trains.
Challenges include high capital requirements, technological infrastructure gaps in developing regions, and high maintenance costs, which can impact the growth and implementation of electrification projects.
Raw materials are carefully sourced based on specifications and quality standards, with inspections conducted to ensure they meet the necessary requirements for building reliable railway electrification structures.
Surface treatments include pickling, galvanization, and coating to protect the structures from corrosion and enhance their durability and performance in various environmental conditions.
Quality assurance involves continuous monitoring, in-process inspections, and final product testing to ensure that all railway electrification structures comply with industry standards and customer specifications.
Future trends include increased investment in sustainable technologies, advancements in electrification infrastructure, and expanded global adoption to improve rail transport efficiency and reduce environmental impact.
Why Choose Utkarsh India
-
With forty years of experience in steel fabrication, galvanisation, plastic extrusion, and moulding, Utkarsh India stands out as a leader in infrastructural manufacturing.
-
Our railway electrification structures feature expert engineering, ensuring reliable and efficient performance for diverse rail systems and applications.
-
We use high-quality steel and aluminium alloys, providing durability and corrosion resistance to withstand challenging environmental conditions.
-
Our advanced manufacturing process includes precise fabrication and rigorous quality checks, guaranteeing top-notch performance and adherence to industry standards.
-
We apply innovative surface treatments like galvanization, enhancing corrosion resistance and extending the lifespan of our railway electrification structures.
-
We implement comprehensive quality control measures throughout production, ensuring each structure meets stringent safety and performance standards.
-
With extensive market expertise, we understand the latest trends and requirements, positioning us as a leader in railway electrification solutions.
-
Our customer-centric approach focuses on tailored solutions, addressing specific needs and providing exceptional support throughout the project lifecycle.