Crash Barriers
Crash barriers are essential safety installations designed to protect motorists and pedestrians by minimising the severity of accidents. These barriers absorb impact energy, prevent vehicles from crossing into oncoming traffic or veering off the road, and safeguard infrastructure. Widely installed on highways, bridges, urban roads, and industrial zones, crash barriers are indispensable for enhancing road safety and reducing fatalities.
There are several types of crash barriers, each tailored to specific applications and safety requirements. W-Beam Crash Barriers, with their characteristic "W" shape, are commonly used on highways and rural roads for their cost-effectiveness and reliability. Thrie Beam Crash Barriers, featuring an additional corrugation, provide enhanced rigidity and containment, making them ideal for high-risk zones like expressways and bridges. Pedestrian Guard Rails, on the other hand, are designed to protect walkways, ensuring the safety of pedestrians in busy urban areas and commercial zones.
Each type of crash barrier is engineered for specific purposes. W-Beam barriers are versatile and can be used on a range of road networks. Thrie Beam barriers are particularly effective in high-speed areas and locations with heavy vehicle traffic, as they provide superior containment. Pedestrian barriers are best suited for sidewalks, crossings, and areas with high foot traffic, preventing accidental vehicle incursions.
Effective crash barriers must meet stringent safety and quality standards. They are designed for durability, high impact resistance, and weather protection, ensuring long-lasting performance in diverse conditions. Features like corrosion resistance, easy installation, and low maintenance make them practical and reliable choices for safety infrastructure. Compliance with global safety norms, such as EN 1317 and MORTH standards, further ensures the reliability of these barriers.
Utkarsh India is a leading manufacturer of crash barriers, setting benchmarks in quality, innovation, and safety. The company offers an extensive range of crash-tested products, including W-Beam, Thrie Beam, and Pedestrian Guard Rails, crafted from premium materials like galvanised steel. Utkarsh’s barriers are known for their exceptional structural integrity, advanced design, and adherence to international standards.
With decades of expertise, Utkarsh India has supplied crash barriers for numerous prestigious projects, including highways, expressways, and industrial zones across India. The company’s commitment to road safety is evident in its rigorous testing processes, in-house manufacturing capabilities, and use of high-grade raw materials from trusted suppliers like TATA and SAIL. Utkarsh’s crash barriers are not only a testament to engineering excellence but also a pledge to make journeys safer for all.
-
144000
Cumulative Crash Barrier Production Capacity
-
5000
Ready Stock
-
H2
Containment Level
- Material Quality Crafted from premium-grade galvanised steel sourced from trusted suppliers like TATA and SAIL, ensuring durability, corrosion resistance, and reliability for long-term performance.
- Design Compliance Utkarsh India’s crash barriers adhere to EN 1317 and IRC 119 standards, guaranteeing exceptional safety and effectiveness for diverse road and industrial applications.
- Load Bearing Capacity Our W-Beam and Thrie Beam barriers are engineered to withstand high-impact forces, ensuring optimal containment and redirection of vehicles upon collision.
- Precision Engineering Designed with advanced CNC machinery, our barriers ensure accurate dimensions, superior finishing, and compliance with specifications for seamless installations.
- Corrosion Resistance Featuring zinc coatings of 99.995% purity, Utkarsh India’s barriers are built to endure harsh weather conditions, offering unmatched longevity and reduced maintenance costs.
- Customisation Options As a leading crash barrier manufacturer in India, we offer custom lengths, profiles, and end treatments tailored to specific project needs and road geometries.
- Safety Tested Our crash barriers undergo rigorous crash testing at NATRAX facilities, conforming to global safety standards like MORTH Clause 810 and European EN 1317 specifications.
- Ready Availability With over 5,000 MT in ready stock, Utkarsh India ensures prompt delivery, establishing itself as a trusted crash barrier supplier for projects across India.
- Impact Resistance Utkarsh India’s crash barriers are engineered for high impact resistance, ensuring maximum safety and protection in collision scenarios.
- Global Standards Our barriers comply with EN 1317 and IRC 119, solidifying our position as a top crash barrier manufacturer in India.
- Enhanced Safety Advanced designs, including W-Beam and Thrie Beam, provide superior containment, reducing accident severity and ensuring reliable road safety solutions.
- Versatile Applications Designed for highways, bridges, and pedestrian zones, our barriers offer adaptable solutions for diverse environments and safety requirements.
- Quick Installation Simplified designs ensure easy installation, making Utkarsh India the preferred crash barrier supplier for large-scale projects with tight deadlines.
- Eco-Friendly Design Constructed with sustainable processes and durable materials, our crash barriers minimise environmental impact, aligning with global sustainability standards.
- Innovative Engineering Incorporating precision manufacturing techniques, our barriers deliver unmatched performance, durability, and reliability for modern road safety infrastructure.
Our Projects
Market Growth
The global crash barrier market is experiencing significant growth, driven by the rising need for road safety and infrastructure development. Valued at approximately USD 6.5 billion in 2023, the market is expected to reach USD 9.8 billion by 2030, growing at a steady CAGR of 6.1%. This surge is fueled by government initiatives worldwide to reduce road fatalities through enhanced safety infrastructure, including crash barriers.
One of the primary factors driving this growth is the increasing implementation of stringent road safety regulations. With an emphasis on reducing accidents and safeguarding motorists, the demand for high-performance crash barriers, such as W-Beam and Thrie Beam, is steadily rising. These barriers, engineered to absorb impact energy and prevent crossover accidents, are becoming essential in highway and urban road projects globally.
The market is also witnessing advancements in materials and technology. Innovations like high-strength galvanised steel and eco-friendly manufacturing processes are setting new benchmarks for durability and sustainability. Additionally, the adoption of global safety standards such as EN 1317 and MORTH further underscores the industry's commitment to reliability and safety compliance.
Utkarsh India aligns perfectly with these market trends, offering a comprehensive range of crash barriers designed to meet evolving safety requirements. Leveraging state-of-the-art manufacturing facilities and high-grade raw materials sourced from TATA and SAIL, Utkarsh India delivers products that excel in quality, durability, and compliance with global standards.
As a trusted crash barrier manufacturer in India, Utkarsh India not only contributes to road safety but also supports infrastructure development with innovative, sustainable solutions. With a proven track record in prestigious projects and a strong focus on market needs, Utkarsh India is well-positioned to lead the crash barrier industry into a safer future.
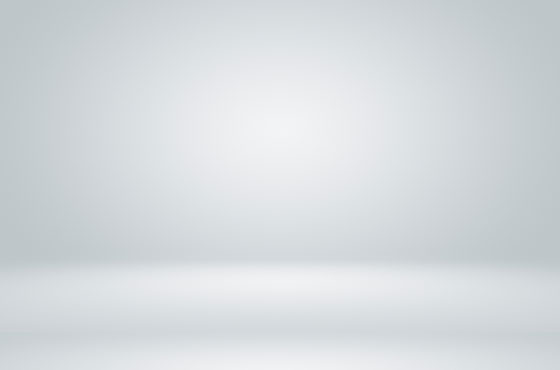
Manufacturing Process
-
Review Technical Documents
Our process begins by meticulously reviewing technical documents to ensure adherence to thrie beam crash barrier specifications and client requirements.
-
Raw Material Inspection
We conduct thorough inspections of raw materials, ensuring they meet the necessary standards for durability and performance.
-
Raw Material Testing (Mechanical & Chemical Test)
Raw materials undergo several mechanical and chemical tests to verify their properties, ensuring high-quality production and reliability.
-
Slitting
In this stage, large rolls of raw material are cut into narrow strips of precise widths to form barrier sections. This ensures precise dimensions and readiness for the subsequent forming stage and assembly.
-
Rolling
Steel coils are fed into rolling mills where they are shaped into specific profiles for thrie-beam production. This is the process that lends the necessary curvature and structural shape of the barriers.
-
Profiling
The barrier is cut into the exact length based on customer requirements to ensure proper fitment and performance of the product when installed. (is this the same as slitting)
-
Stamping
This step is done based on customer requirements and involves using dies to imprint specific designs or features onto the barrier surface.
-
Galvanising
- Pickling in Caustic Soda Solution HR coils are immersed in a caustic soda solution to remove any impurities and scale from the surface.
- Rinsing in Water House The coils are then rinsed thoroughly in a water house to remove residual caustic soda solution.
- Pickling in Acid Tank Next, the coils undergo pickling in an acid tank to further clean and prepare the surface for galvanisation.
- Rinsing in Water Tank Coils are rinsed again in a water tank to neutralise any remaining acid.
- Pre-fluxing This involves applying a flux solution to the surface of the coils, which helps in the adhesion of the zinc coating.
- Drying in Hot Chamber The coils are dried in a hot chamber to remove any moisture before galvanisation.
- Hot Dip Galvanisation in Zinc Bath The dried coils are immersed in a zinc bath at high temperatures, ensuring uniform surface coating of zinc.
- Cooling in Quenching Tank of White Water The galvanised coils are then cooled in a quenching tank filled with white water to solidify the zinc coating.
- Cooling in Quenching Tank of DI-Chromate Water The coils undergo further cooling in a quenching tank filled with DI-chromate water to enhance corrosion resistance and improve surface finish.
-
Finishing and quality checks
The finished coils are inspected for quality to ensure the galvanization coating layer is even and as required. Trimming is done if required to ensure the final producy dimensions. (CHECK THAT NO ROLL FORMING HERE AS PREVIOUSLY WRITTEN) Rigorous testing is also conducted while completing all the previously listed steps such as dimensional checks, visual inspections for defects, and testing for structural integrity of the barriers.
-
Packing
This stage involves packing the goods securely, labelling them correctly, and ensuring all required documentation (such as invoices and shipping labels) is completed. The goal is to ensure the items are protected during transit and all necessary information is provided for smooth delivery.
-
Despatch
Once packed, the goods are transferred to a shipping carrier or logistics provider. This phase includes managing logistics, tracking the shipment, and ensuring timely delivery to the destination, as well as handling any potential issues that may arise during transportation.
Quality Policies
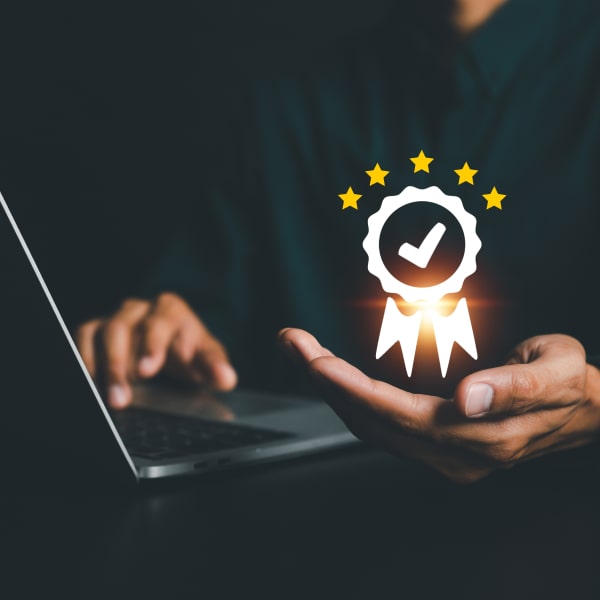
FAQs
Utkarsh India’s crash barriers are manufactured using high-grade galvanised steel sourced from trusted suppliers like TATA and SAIL, ensuring durability and corrosion resistance.
We manufacture W-Beam, Thrie Beam, and Pedestrian Guard Rails, each designed for specific applications like highways, urban roads, industrial zones, and pedestrian areas.
Crash barriers absorb impact energy during collisions, preventing vehicles from crossing lanes or veering off the road, thus enhancing road safety.
Thrie Beam barriers have an additional corrugation for enhanced rigidity and containment, making them ideal for high-risk areas like bridges and expressways.
Yes, our crash barriers adhere to standards like EN 1317, IRC 119, and MORTH Clause 810, ensuring superior safety and reliability.
Yes, our barriers feature a 99.995% zinc coating, providing excellent corrosion resistance and durability in extreme weather conditions.
Our state-of-the-art manufacturing facilities, adherence to global standards, and extensive project expertise make us a trusted name in the industry.
Our barriers undergo rigorous crash testing at facilities like NATRAX, ensuring compliance with safety standards and optimal performance.
Yes, we offer customisation in terms of length, profile, and end treatments to suit unique project requirements and road geometries.
We maintain over 5,000 MT of ready stock, ensuring prompt delivery for large-scale infrastructure projects across India.
Our barriers are used on highways, bridges, urban roads, industrial zones, railway crossings, and pedestrian walkways to enhance safety.
We use Fe360, Fe410, and Fe510 grades of steel, meeting IS and BS standards for structural integrity and long-lasting performance.
Our manufacturing process includes eco-friendly practices, and the use of high-quality materials ensures long lifespans, reducing environmental impact.
W-Beam barriers typically have a width of 312 mm, while Thrie Beam barriers measure 502 mm, providing superior coverage and protection.
We have contributed to prestigious projects like the Bharatmala Pariyojana, NHAI roadways, industrial zones, and many more urban safety infrastructure development projects.
Why Choose Utkarsh India
-
With over forty years in steel fabrication, galvanisation, plastic extrusion, and moulding, Utkarsh India has established itself as a leader in infrastructural manufacturing.
-
We are the largest Indian manufacturer of crash barriers, operating two state-of-the-art plants with a monthly capacity of 12,000 MT (500 Km).
-
We source the best quality raw materials through monthly MOUs with reputed vendors like SAIL and Hindustan Zinc, ensuring consistent supply and superior product quality.
-
Our advanced in-house laboratories conduct rigorous quality checks on both raw materials and finished products, guaranteeing the highest standards.
-
Our dedicated logistics team operates 24/7, ensuring a swift delivery period of 1-2 days across India. We maintain a ready stock of 50 km of crash barriers at all times.
-
With four 12.8-meter-long in-house galvanisation units, boasting a 12,000 MT/month capacity, we use 99.9% pure zinc to deliver the best quality galvanised iron (GI).
-
Our materials comply with stringent quality norms set by Indian boards (MORTH, IRC) and American boards (AASHTO) and have been crash tested to meet European standards (EN 1317-2).
-
We excel in managing vendor relationships, supported by dedicated after-sales assistance and support.