Bridges and Urban Roads
Ensuring safety on bridges and urban road networks demands robust, high-performance solutions capable of addressing unique infrastructural challenges. Our Thrie Beam crash barriers are precisely engineered to meet these needs, integrating advanced features and technical specifications for superior protection in diverse environments.
Designed to comply with MoRTH clause 810 and IRC standards, our barriers are engineered to withstand significant impacts, tested for vehicles up to 13,000 kgs. Constructed with a thickness of 2.8mm and high-grade steel (Fe360, Fe410, and Fe510), they offer best-in-class durability. The use of Special High Grade Zinc (99.995%) ensures superior corrosion resistance, enhancing the barriers' longevity and performance.
On bridges, these barriers maintain structural integrity while managing high-speed traffic and environmental stresses, providing reliable containment and safety. In urban road networks, their versatile design meets the challenges of varying traffic conditions, offering effective protection for both vehicles and pedestrians.
Our Thrie Beam crash barriers are trusted for their resilience and compliance with stringent standards, ensuring enhanced safety and reliability on bridges and urban roadways.
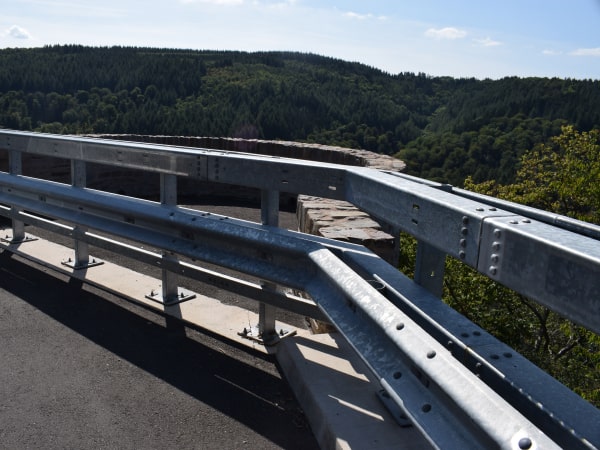
Related Products
Discover other top-quality products from our range that are customised to meet your needs and exceed expectations. Explore now!
Manufacturing Process
Our meticulous, research-backed manufacturing process ensures durability, safety, and precision in every Thrie Beam Crash Barriers.
-
Pickling in Caustic Soda Solution
HR coils are immersed in a caustic soda solution to remove any impurities and scale from the surface.
-
Rinsing in Water House
The coils are then rinsed thoroughly in a water house to remove residual caustic soda solution.
-
Pickling in Acid Tank
Next, the coils undergo pickling in an acid tank to further clean and prepare the surface for galvanization.
-
Rinsing in Water Tank
Coils are rinsed again in a water tank to neutralise any remaining acid.
-
Pre-fluxing
This involves applying a flux solution to the surface of the coils, which helps in the adhesion of the zinc coating.
-
Drying in Hot Chamber
The coils are dried in a hot chamber to remove any moisture before galvanisation.
-
Hot Dip Galvanization in Zinc Bath
The dried coils are immersed in a zinc bath at high temperatures, ensuring uniform surface coating of zinc.
-
Cooling in Quenching Tank of White Water
The galvanised coils are then cooled in a quenching tank filled with white water to solidify the zinc coating.
-
Cooling in Quenching Tank of DI-Chromate Water
The coils undergo further cooling in a quenching tank filled with DI-chromate water to enhance corrosion resistance and improve surface finish.
Quality Policies
Discover our cutting-edge infrastructure and commitment to unparalleled quality standards.
-
State-of-The-Art Machinery
Advanced infrastructure and cutting-edge machinery to ensure precision engineering and adherence to stringent quality standards.
-
Premium-Grade Sourcing
Meticulous selection of industry-leading raw materials guarantees integrity, durability, and superior performance of our products.
-
Quality Management
From production to testing, our unwavering commitment to quality control ensures compliance with the highest technical specifications and industry standards, reaffirming our position as the partner of choice for the best thrie beam metal crash barriers in India.
Testing Videos
Watch how our products are rigorously tested for maximum safety assurance.
FAQs
A. Thrie Beam barriers stand out from other types of barriers due to their unique design and superior effectiveness. Unlike conventional W-Beam barriers, Thrie Beam barriers feature an extra corrugation, resulting in enhanced rigidity and durability. This distinct construction makes Thrie Beam barriers especially adept at preventing smaller vehicles from penetrating through the barrier. The additional corrugation significantly boosts the barrier's ability to contain and redirect vehicles upon impact, rendering Thrie Beam barriers the preferred option for scenarios requiring heightened containment and redirection measures.
Our thrie Beam crash barriers are manufactured using high-quality galvanised steel. We utilise premium-grade steel with specific mechanical properties to ensure optimal strength, durability, and corrosion resistance. This galvanised steel construction provides long-term protection against rust and maintains structural integrity.
Thrie Beam barriers provided by Utkarsh India present a multitude of advantages. With sturdy build quality and compliance with global standards, our barriers guarantee longevity and consistent performance across various settings. Their versatility spans applications on highways, expressways, bridges, urban road networks, industrial zones, railway crossings, and rural roads, establishing them as indispensable elements within comprehensive road safety frameworks.
The efficacy of Thrie Beam barriers hinges upon several factors including design elements, material excellence, compliance with global standards, and meticulous installation procedures.
Yes, thrie beam crash barriers can be customised in terms of length, height, beam profile, and end treatments to meet specific project requirements and accommodate varying road geometries and traffic conditions.
Thrie beam barriers by Utkarsh India are designed to withstand a wide range of weather conditions, including extreme temperatures, heavy rainfall, and high winds. The galvanised steel construction provides corrosion resistance, ensuring durability and reliability even in adverse weather conditions.
The efficacy of Thrie Beam barriers hinges upon several factors including design elements, material excellence, compliance with global standards, and meticulous installation procedures.
Yes, our thrie beam crash barriers are tested and certified to meet national and international safety standards, such as AASHTO M180, EN 1317, and MASH (Manual for Assessing Safety Hardware).
Our thrie beam crash barriers can be installed on curved sections of roads or highways using specialised mounting hardware and installation techniques. The flexibility of thrie beam barriers allows them to conform to the curvature of the road while maintaining their effectiveness in redirecting errant vehicles and enhancing safety.
A.As one of the leading crash barrier manufacturers, our precision-designed thrie beam crash barriers are highly effective in high-speed areas, such as divided highways and medians, in preventing vehicle crossover accidents. Their sturdy construction and design as per standard metal beam crash barrier specifications ensure that vehicles are redirected back into their lanes upon impact, reducing the risk of head-on collisions and improving overall road safety in fast-moving traffic environments.
Indeed, the Thrie Beam barriers from Utkarsh India prioritise environmental friendliness. Constructed with top-notch materials and subjected to a galvanization technique, these barriers deliver resilience and corrosion resistance, reducing the necessity for frequent replacements and upkeep. Utilising galvanised steel from trusted suppliers further guarantees a sustainable and eco-conscious solution.
Utkarsh India has engineered Thrie Beam barriers for streamlined installation across diverse road terrains. Their flexibility and customisable attributes render them appropriate for a range of environments. Opting for professional installation is advised to guarantee precise alignment and spacing, coupled with regular inspections to fine-tune adjustments, thereby enhancing road safety. Rely on Utkarsh India for dependable Thrie Beam barrier installation services.
When deciding between Thrie Beam barriers and other barrier systems for a particular roadway, it's crucial to take into account factors such as the road's surroundings, traffic patterns, and safety standards. Thrie Beam barriers, distinguished by their distinct design and attributes, provide heightened defence and absorb energy more effectively during accidents, rendering them suitable for diverse scenarios. Evaluating the precise requirements of the roadway and seeking advice from professionals can facilitate a well-informed decision that emphasises safety and efficacy.
Utkarsh India's Thrie Beam barriers are crafted from top-tier raw materials procured from renowned brands such as SAIL, TATA, and Hindustan Zinc, guaranteeing exceptional durability and extended lifespan. Manufactured through a cold-rolling process with a thickness of 2.8mm, these materials conform to IS 5986/2062/10748 standards, featuring grades Fe360/Fe410/Fe510 to ensure structural integrity. This meticulous selection of materials contributes to corrosion resistance and consistent performance, aligning with international benchmarks and ensuring the enduring effectiveness of the barriers.
For inquiries regarding Thrie Beam crash barrier maintenance, manufacturer details, crash absorption information, and insights on Thrie Beam metal barrier cost, please don't hesitate to contact us directly.
Why Choose Utkarsh India
-
in steel fabrication, galvanisation, plastic extrusion and moulding, providing all infrastructural & manufacturing requirements under one roof.
-
along with cutting-edge testing facilities and R&D labs, and proven capability to accomplish manufacturing target deadlines.
-
for finished products and raw material storage, ensuring prompt availability and efficient supply chain management, with close connectivity via seaports, national highways and railways.
-
through raw material procurement from leading national and international manufacturers, ensuring responsible sourcing and superior traceability
-
with committed after sales support and assistance, ensuring seamless service and customer satisfaction at every step.
-
With forty years of experience in steel fabrication, galvanisation, plastic extrusion, and moulding, Utkarsh India is a leader in infrastructural manufacturing.
-
Our polygonal poles have undergone rigorous testing, including wind tunnel tests at IIT Kanpur and structural stability assessments from CSIR, Chennai, ensuring suitability for wind speeds up to 250 km/hr.
-
We produce 1000 lighting masts and 25,000 polygonal poles per month, leveraging well-trained manpower and advanced machinery. Our methodical process ensures timely delivery with minimal reworks and flawless finishes.
-
We have strategic procurement ties with SAIL and HZL for HR Coil and Zinc, and with various reputable companies for accessories. Our ready stock of materials ensures prompt production and delivery.
-
We utilise electroplated rope drums to combat corrosion and extend equipment life. All hardware is either made from stainless steel or hot-dip galvanised for enhanced durability.
-
Our five galvanising units employ a 7-tank process, using modern technology and supervised by qualified technicians, ensuring superior quality and longevity of the galvanised products.
-
Our in-house PU painting facility applies a protective and aesthetic coating over galvanised surfaces, enhancing product appearance and providing additional corrosion protection.
-
A dedicated logistics team oversees efficient transportation, with factories strategically located near NHAI, ports, and airports for seamless delivery.
-
Experienced service engineers provide comprehensive after-sales support, offering troubleshooting and technical assistance to ensure client satisfaction.
Related Videos
Explore more with our related videos, showcasing our products, manufacturing processes, solutions and more.