Parking Lot Barriers
Our meticulously designed W Beam Crash Barriers offer exceptional safety solutions for parking lots, where robust vehicle protection is essential. Designed to meet rigorous standards, our barriers are made from high-quality raw materials sourced from industry leaders like TATA and SAIL.
Our range includes Single Side Single Barrier, Double Side Single Barrier, Single Side Double Barrier, and Double Side Double Barrier configurations, ensuring flexibility for various parking lot designs.
Manufactured to comply with both Indian and international safety standards, our barriers feature a cold-rolled thickness of 2.8mm and are constructed from Fe360/Fe410/Fe510 grades. These barriers are crash-tested to handle impacts from vehicles weighing up to 10,000 kg, ensuring they provide reliable protection in high-traffic areas. Our products are also aligned with Euro-standard testing, offering enhanced durability and structural strength.
Incorporating advanced manufacturing techniques and rigorous quality control, our W Beam Crash Barriers provide robust protection against accidental impacts in parking environments.
With quick delivery and a strategic location near major transport routes, we ensure timely service for your parking lot projects.
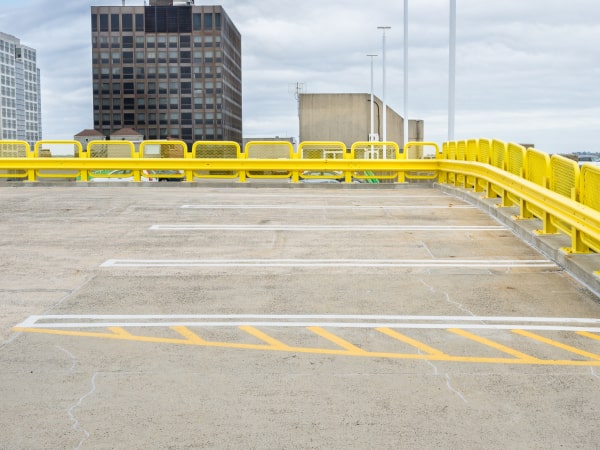
Related Products
Discover other top-quality products from our range that are customised to meet your needs and exceed expectations. Explore now!
Manufacturing Process
Our range of W beam barriers are manufactured to provide a seamless combination of durability, safety, and precision, so that they deliver optimal performance.
-
Pickling in Caustic Soda Solution
HR coils are immersed in a caustic soda solution to remove any impurities and scale from the surface.
-
Rinsing in Water House
The coils are then rinsed thoroughly in a water house to remove residual caustic soda solution.
-
Pickling in Acid Tank
Next, the coils undergo pickling in an acid tank to further clean and prepare the surface for galvanization.
-
Rinsing in Water Tank
Coils are rinsed again in a water tank to neutralise any remaining acid.
-
Pre-fluxing
This involves applying a flux solution to the surface of the coils, which helps in the adhesion of the zinc coating.
-
Drying in Hot Chamber
The coils are dried in a hot chamber to remove any moisture before galvanisation.
-
Hot Dip Galvanization in Zinc Bath
The dried coils are immersed in a zinc bath at high temperatures, ensuring uniform surface coating of zinc.
-
Cooling in Quenching Tank of White Water
The galvanised coils are then cooled in a quenching tank filled with white water to solidify the zinc coating.
-
Cooling in Quenching Tank of DI-Chromate Water
The coils undergo further cooling in a quenching tank filled with DI-chromate water to enhance corrosion resistance and improve surface finish.
Quality Policies
Discover our cutting-edge infrastructure and commitment to unparalleled quality standards.
-
Cutting-Edge Infrastructure
Our state-of-the-art facilities are equipped with advanced machinery and in-house testing laboratories. This infrastructure enables us to execute precise engineering, ensuring that every W beam crash barrier meets stringent quality standards. By maintaining cutting-edge technology and processes, we consistently deliver products that exceed industry expectations.
-
Raw Material Sourcing
As the best W beam crash barrier manufacturers in India, we meticulously source our raw materials from industry leaders such as TATA and SAIL. This commitment to using premium-grade materials ensures that our W beam crash barriers are manufactured with the highest standards of quality and durability. Each component undergoes rigorous checks to maintain the precision and reliability required for top-tier crash barriers.
-
Stringent Testing
Our W beam crash barriers undergo rigorous testing to meet Indian, European, and American standards. This comprehensive testing process includes various crash simulations and performance evaluations to ensure that our products offer superior durability and safety. Our commitment to stringent testing guarantees that every barrier performs optimally under real-world conditions.
Testing Videos
Watch how our products are rigorously tested for maximum safety assurance.
FAQs
W-beam crash barriers and guardrails are frequently considered synonymous. The term 'W-beam' denotes the shape of the barrier rail, which is commonly referred to as a guardrail. These safety barriers along roadsides are engineered to safeguard and deter vehicles from veering off the roadway during accidents, serving as a crucial safety feature across diverse transportation networks.
According to W beam crash barrier specifications offered by Utkarsh India, our products provide several benefits, including improved road safety, reduced risk of head-on collisions, protection of motorists and pedestrians, and minimise damage to vehicles and infrastructure in the event of accidents.
Being the top W-beam crash barriers manufacturer in India, we offer products available in a variety of lengths to adapt to various road configurations and project demands. Utkarsh India, a prominent manufacturer of W-beam crash barriers, provides a selection of lengths to ensure versatility and compatibility across a range of applications. This assortment of lengths facilitates efficient customisation according to individual project requirements and road designs.
W-beam crash barriers are engineered to deliver optimal impact resistance, safeguarding structural integrity and sustaining protection over time. The level of impact resistance is contingent upon various factors such as design intricacies and material composition, all of which adhere rigorously to safety standards.
Utkarsh India’s W type beam crash barriers are designed to withstand high-impact forces and harsh weather conditions, making them highly durable and long-lasting. They are typically made of galvanised steel to resist corrosion and maintain structural integrity over time.
When selecting W beam crash barriers, factors such as road design, traffic volume, speed limits, terrain conditions, and environmental factors should be considered to ensure optimal performance and compliance with safety standards.
Yes, W beam crash barriers can be customised in terms of length, height, beam profile, and end treatments to meet specific project requirements and accommodate varying road geometries and traffic conditions.
W beam crash barriers typically consist of W-shaped steel beams, posts, and connecting hardware. These components work together to absorb impact energy and prevent vehicles from crossing into opposing lanes or off the road.
Following a collision, W-beam metal crash barriers are engineered to incur minimal bending or deflection, thereby preserving their structural integrity and sustained protection. The extent of deflection is contingent upon variables such as the barrier's design and the materials utilised, in accordance with safety protocols. These barriers are meticulously crafted to absorb crashes, serving as a crucial safety precaution in collision scenarios.
Maintenance of W-beam crash barriers involves conducting regular inspections to identify any damage or signs of wear, along with routine checks to ensure that the barriers are maintained in optimal condition, thus ensuring consistent and reliable protection. Additionally, regular cleaning to eliminate debris and the implementation of corrosion prevention measures are essential practices that contribute to the durability and effectiveness of W-beam crash barriers.
W-beam crash barriers are subjected to standardised crash tests to verify their safety and efficacy. These assessments scrutinise aspects such as deflection, structural integrity, and their capacity to redirect or confine a vehicle upon impact. Adherence to international safety standards, encompassing regulations established by Indian, American, and European authorities, attests to the quality and dependability of W-beam crash barriers, affirming their established safety credentials.
W-beam crash barriers are subjected to standardised crash tests to verify their safety and efficacy. These assessments scrutinise aspects such as deflection, structural integrity, and their capacity to redirect or confine a vehicle upon impact. Adherence to international safety standards, encompassing regulations established by Indian, American, and European authorities, attests to the quality and dependability of W-beam crash barriers, affirming their established safety credentials.
The expenses associated with installing crash barriers fluctuate depending on variables such as project scope, site location, and unique demands. Generally, these expenses cover materials, workforce, machinery, and any supplementary components such as terminals or transitions. Utkarsh India delivers tailored solutions and is capable of furnishing comprehensive cost assessments tailored to individual project requirements.
Our W Beam crash barriers are designed with environmental sustainability in mind. As the most trusted W beam crash barrier manufacturers. We utilise galvanised steel, which is a highly recyclable material, reducing the environmental footprint associated with manufacturing. Additionally, our barriers are engineered to minimise roadside vegetation disruption and habitat fragmentation, preserving the natural ecosystem.
W-beam crash barriers, made of galvanised steel, provide flexibility and absorb energy during accidents, effectively redirecting vehicles for increased safety. Conversely, concrete barriers, being rigid, can result in more significant damage upon collision. The decision between the two depends on variables such as the road environment, traffic conditions, and safety standards.
Our W Beam crash barriers are manufactured using high-quality galvanised steel. We use premium-grade steel with specific mechanical properties, ensuring optimal strength, durability, and corrosion resistance. This galvanised steel construction to ensure crash barrier quality that provides long-term protection against rust and ensures the barriers maintain their structural integrity even in harsh environmental conditions, enhancing overall safety and reliability on the roads.
Why Choose Utkarsh India
-
in steel fabrication, galvanisation, plastic extrusion and moulding, providing all infrastructural & manufacturing requirements under one roof.
-
along with cutting-edge testing facilities and R&D labs, and proven capability to accomplish manufacturing target deadlines.
-
for finished products and raw material storage, ensuring prompt availability and efficient supply chain management, with close connectivity via seaports, national highways and railways.
-
through raw material procurement from leading national and international manufacturers, ensuring responsible sourcing and superior traceability
-
with committed after sales support and assistance, ensuring seamless service and customer satisfaction at every step.
-
With forty years of experience in steel fabrication, galvanisation, plastic extrusion, and moulding, Utkarsh India is a leader in infrastructural manufacturing.
-
Our polygonal poles have undergone rigorous testing, including wind tunnel tests at IIT Kanpur and structural stability assessments from CSIR, Chennai, ensuring suitability for wind speeds up to 250 km/hr.
-
We produce 1000 lighting masts and 25,000 polygonal poles per month, leveraging well-trained manpower and advanced machinery. Our methodical process ensures timely delivery with minimal reworks and flawless finishes.
-
We have strategic procurement ties with SAIL and HZL for HR Coil and Zinc, and with various reputable companies for accessories. Our ready stock of materials ensures prompt production and delivery.
-
We utilise electroplated rope drums to combat corrosion and extend equipment life. All hardware is either made from stainless steel or hot-dip galvanised for enhanced durability.
-
Our five galvanising units employ a 7-tank process, using modern technology and supervised by qualified technicians, ensuring superior quality and longevity of the galvanised products.
-
Our in-house PU painting facility applies a protective and aesthetic coating over galvanised surfaces, enhancing product appearance and providing additional corrosion protection.
-
A dedicated logistics team oversees efficient transportation, with factories strategically located near NHAI, ports, and airports for seamless delivery.
-
Experienced service engineers provide comprehensive after-sales support, offering troubleshooting and technical assistance to ensure client satisfaction.
Related Videos
Explore more with our related videos, showcasing our products, manufacturing processes, solutions and more.